Environmental Factors >
Sustainable Procurement and Supplier Management
Sustainable Procurement and Supplier Management
Sustainable Procurement
To deepen the root for sustainability ideas and incorporate them in our procurement practice, and to work with suppliers to take advantage of the opportunity to jointly create values, FFHC has introduced the "ISO 20400:2017 Sustainable Procurement-Guidance" since 2020, and implemented the seven core themes in our procurement practice. We completed the "Performance Assessment for ISO 20400 Sustainable Procurement-Guidance" in November 2023, and received a certificate as well as a respectable Level 4 rating. The green procurement target for 2023 was NT$80 million, and the actual procurement amount was NT$115.17 million. We have been verified as a benchmark organization for "green procurement by private enterprises and organizations" by the Taipei City Government for 9 consecutive years, in addition to honoring our green procurement commitment to the Coalition of Movers and Shakers on Sustainable Finance.
Process for Introducing the ISO 20400:2017 Sustainable Procurement Guidance
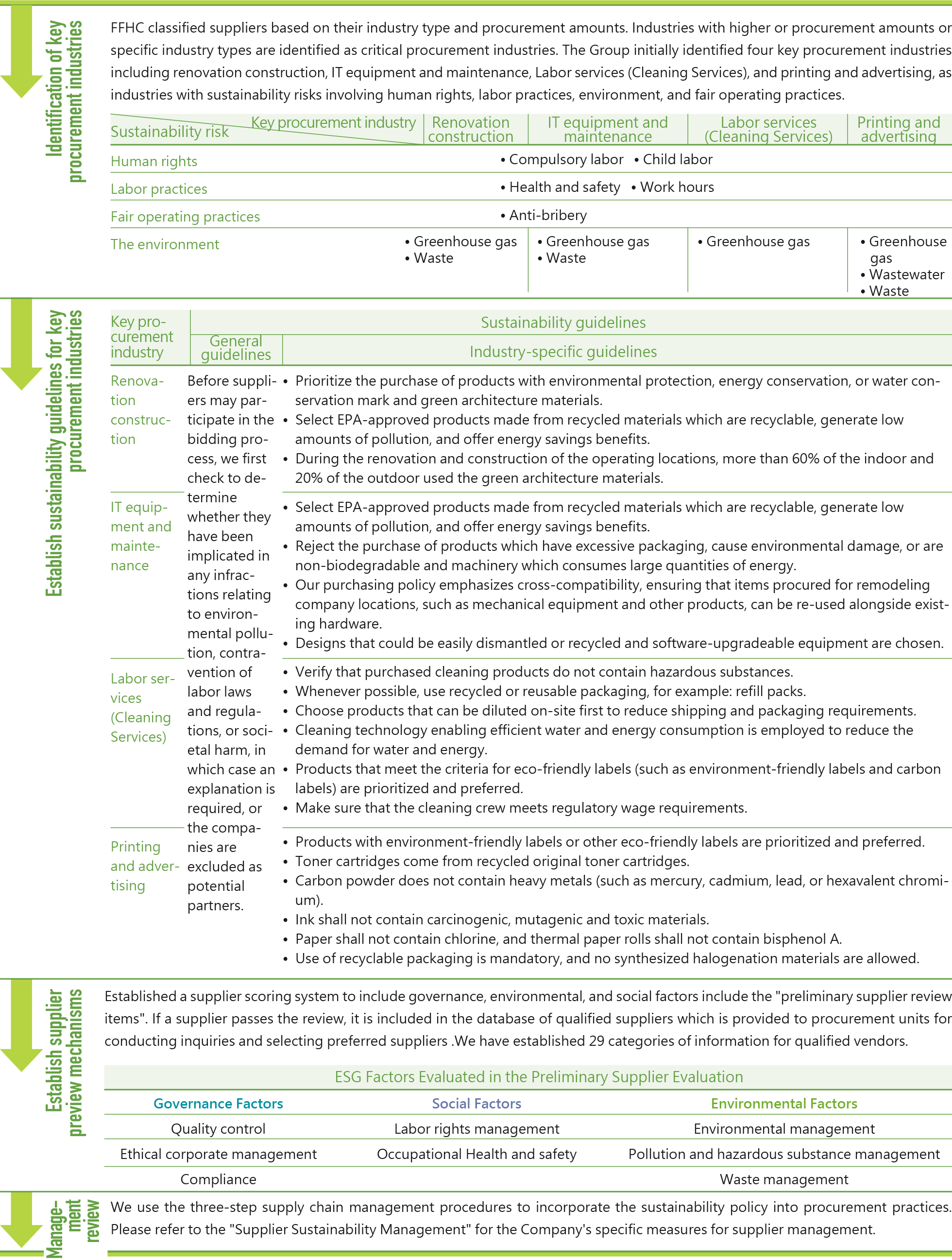
Supplier Sustainability Management
FFHC established the "Supplier Management Guidelines" as the policy and guiding principles for the management of suppliers of the Group. We require suppliers to comply with the Guidelines when signing contracts and we require suppliers to sign the "Human Rights and Environmental Sustainability Clauses" and to increase awareness. We also require subsidiaries to use site visits and audits to encourage suppliers to implement the Guidelines. The contents include basic labor rights for suppliers, environmental protection, sustainable management, and occupational safety and health regulations.
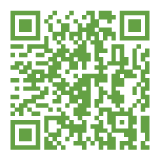
FFHC set up a 3-step supply chain management process in 2013, supplier management is used to select vendors that satisfy the spirit of sustainable development as long-term partners, including: purchasing of energy-saving equipment, purchasing and maintenance of IT equipment, construction and interior design, business-related OA equipment and landscape and environmental greening engineering. As a principle, the main procurement regions include suppliers of the place country of operations and those close to business locations. In 2023 100%*1 of all purchasing came from local suppliers*2 to ensure the stability and localization of the supply chain as well as reduce carbon emissions in the transportation process and create local job opportunities.
To realize an environmentally responsible business model and to actively build up green supply chains, FFHC has enhanced our supplier ESG risk management since 2022. ESG risk factors have been added to our audit items, and we also conduct investigations into suppliers from whom we spend a large amount of money purchasing goods. In March 2023, we conducted supplier GHG inventories and the negotiating meeting for climate risk management, as we guided suppliers to gradually complete their carbon footprint verification. In July, the "Supplier GHG Inventory Platform" was completed and went online. 192 information equipment, maintenance, printing and publicity vendors with more than NT$1 million in procurement amount as well as business dealings with the Company within the previous two years had been chosen. These suppliers were asked to visit the platform and fill in information pertaining to Scope 1 (gasoline consumption) and Scope 2 (electricity consumption) for GHG emissions. A total of 69 vendors have submitted their data, as we continue to push for vendors' carbon footprint verification and the formulation of carbon reduction targets, as part of our efforts to refine our supply chains' low carbon management.
To realize an environmentally responsible business model and to actively build up green supply chains, FFHC has enhanced our supplier ESG risk management since 2022. ESG risk factors have been added to our audit items, and we also conduct investigations into suppliers from whom we spend a large amount of money purchasing goods. In March 2023, we conducted supplier GHG inventories and the negotiating meeting for climate risk management, as we guided suppliers to gradually complete their carbon footprint verification. In July, the "Supplier GHG Inventory Platform" was completed and went online. 192 information equipment, maintenance, printing and publicity vendors with more than NT$1 million in procurement amount as well as business dealings with the Company within the previous two years had been chosen. These suppliers were asked to visit the platform and fill in information pertaining to Scope 1 (gasoline consumption) and Scope 2 (electricity consumption) for GHG emissions. A total of 69 vendors have submitted their data, as we continue to push for vendors' carbon footprint verification and the formulation of carbon reduction targets, as part of our efforts to refine our supply chains' low carbon management.
*1:Calculated based on the 503 suppliers with whom the Group conducted transaction in 2023.
*2:Local refers to countries in which various locations of operations are based.
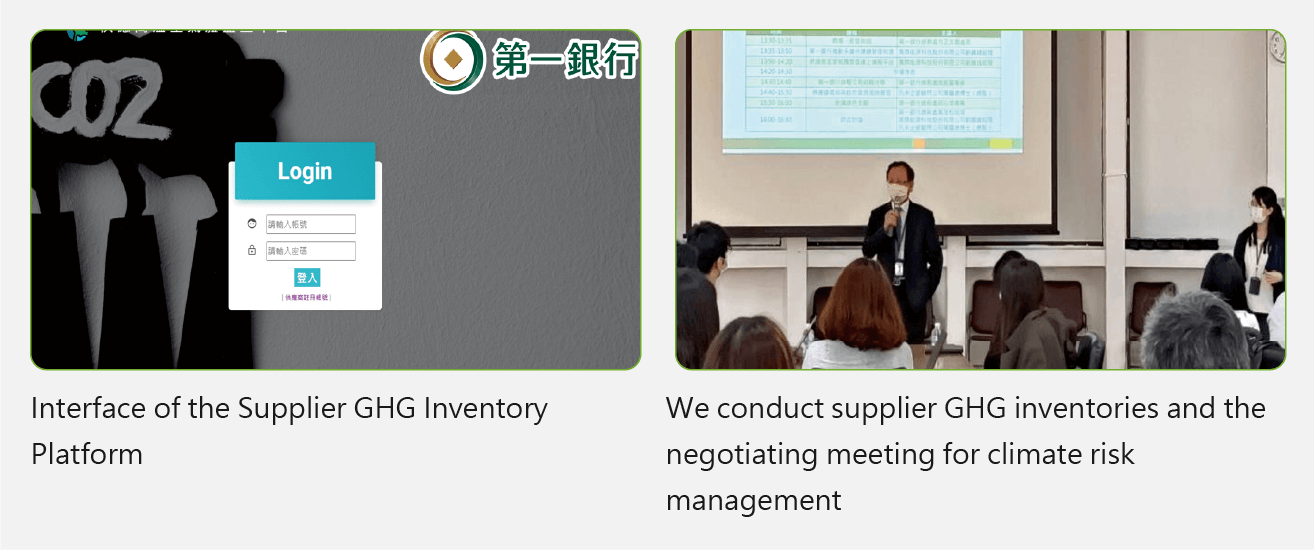
■ 3-step Supply Chain Management Process
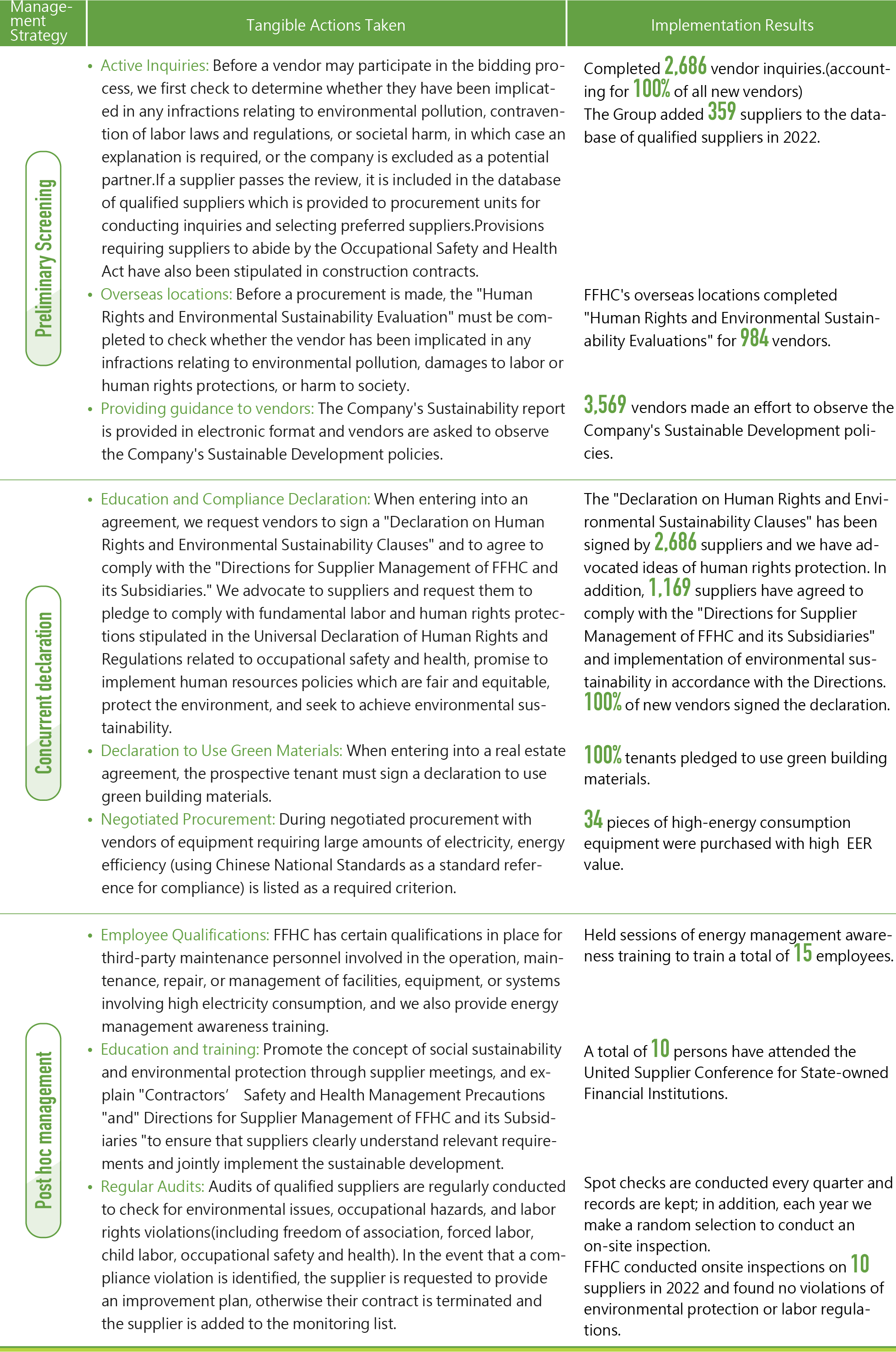
■ Assessed whether suppliers have violated issues related to human rights and percentage of mitigation measures that have been implemented.

*1:We compiled statistics using the number of suppliers in 2023. Among 503 suppliers, we identified 218 suppliers with human rights violation risks, including seven suppliers in the clothing category prone to occupational hazards such as muscle and bone injuries, three suppliers in the moving company category, 99 suppliers in the renovation category, 24 suppliers in the air conditioning category, 58 suppliers in the plumbing engineering category, 17 suppliers in the fire protection engineering category, six suppliers in the landscape engineering category, and four suppliers in the solar power generation engineering category.
*2:There were no cases where suppliers of the Company received penalties for violation of labor laws before signing contracts or within the contract duration and failed to make improvements. Therefore, there were no records of termination of partnerships with suppliers.
■ Identification of key suppliers' potential environmental and social impacts and their improvement rates
・Prior to tender opening in 2023, the Company had evaluated 192 key suppliers (with over NT$1 million in procurement) with respect to their potential environmental and social impacts.
・We looked into the suppliers that had been identified as having materially substantial or potentially negative impact on environment and society. We found that none of them had violated regulations pertaining to environmental protection, labor protection, or occupational safety and health.
・After our evaluation and investigation, the above-mentioned suppliers were not involved in any regulatory violations in 2023. Therefore, no contracts were terminated.